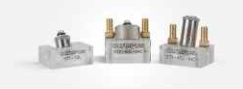
NM01ST270LHDPEIHC
ST2 HDPE Wedge, 70°, IHC, AOD, ULSO "70° ONLY"
Choose Quantity
The ULSO ST2 HDPE Wedge, 70°, IHC, AOD is a specialized ultrasonic transducer wedge crafted from High-Density Polyethylene (HDPE), meticulously designed to facilitate accurate and efficient ultrasonic inspections on curved surfaces, specifically the outside diameter (AOD) of pipes or tubes. This wedge is engineered to provide a refracted ultrasonic beam at a nominal angle of 70 degrees within the test material (typically steel, though the actual refracted angle will depend on the material's acoustic velocity).
The use of HDPE as the wedge material offers a good balance of acoustic impedance matching with many common test materials, ensuring efficient transmission of the ultrasonic pulse. Its machinability also allows for precise shaping of the wedge to achieve the desired beam angle and curvature.
The designation 70° indicates the intended refracted angle of the ultrasonic beam, most likely a shear wave, within the material being inspected when used with a compatible ultrasonic transducer. A 70-degree shear wave angle is a common choice in non-destructive testing (NDT) for detecting and characterizing flaws that have a significant vertical component or are oriented at angles that are optimally interrogated by this steeper beam path. However, depending on the specific application and transducer used with the ST2 wedge, it could also be configured for a 70-degree longitudinal wave, particularly in techniques like Time-of-Flight Diffraction (TOFD).
The inclusion of the IHC suffix highlights three key integrated features designed to enhance the wedge's performance and durability:
Irrigation (I): The wedge is equipped with internal channels or ports that enable the introduction of ultrasonic couplant, typically water, directly to the critical interfaces between the transducer and the wedge, and between the wedge and the curved surface of the pipe or tube. This integrated irrigation system ensures consistent and effective acoustic coupling, which is essential for reliable ultrasonic signal transmission and reception, especially during circumferential scans or automated inspections.
Holes (H): The wedge incorporates strategically placed mounting holes that allow for secure and stable attachment to various manual or automated scanning devices and fixtures. This feature ensures consistent probe positioning and controlled movement during the inspection process, contributing to data repeatability and accuracy.
Carbides (C): The contact surface of the wedge, which conforms to the outside diameter of the pipe or tube, is enhanced with embedded carbide wear pins or a durable carbide facing. Carbide is an exceptionally hard and abrasion-resistant material. The integration of carbides significantly increases the wedge's resistance to wear, especially during circumferential scanning over potentially rough or scaled pipe surfaces. This prolongs the lifespan of the wedge and helps maintain consistent acoustic coupling characteristics over time.
The AOD (Axial Outside Diameter) designation is crucial, indicating that the contact surface of the ST2 wedge is specifically contoured to match a particular outside diameter of a pipe or tube. This curved design ensures optimal surface contact and consistent couplant film thickness, which are vital for efficient and reliable ultrasonic coupling when inspecting cylindrical components, typically for circumferential weld inspections or corrosion mapping.