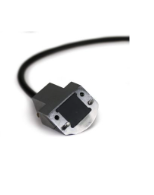
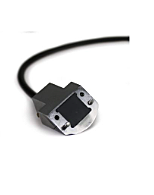
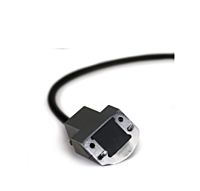
NM01X0AW00115IH
The Sonatest X0AW-N45S-IHC Shear Wave Wedge is a high-performance accessory engineered to optimize phased array ultrasonic testing on curved surfaces. This precision-designed wedge generates a 45° shear wave within the test material (typically steel), a critical angle for effectively detecting transverse cracks and other common weld defects.
Featuring an outer diameter (OD) radius of 1.5 inches, this wedge provides excellent acoustic coupling and stable scanning on pipes and other cylindrical components with a corresponding curvature (e.g., 3" OD pipes). The -IHC designation indicates the inclusion of an integrated irrigation system, which facilitates consistent and reliable ultrasonic transmission, particularly beneficial for automated or encoded scanning applications where maintaining continuous contact is crucial.
This is a direct contact wedge with a 0 mm delay line, maximizing signal transmission efficiency and providing excellent near-surface resolution. The wedge is cut at a precise 31° angle to achieve the desired 45° shear wave refraction in steel. Designed for seamless integration with Sonatest phased array transducers, the X0AW-N45S-IHC ensures optimal performance and data quality.
Key Features:
Optimized for Curved Surfaces: 1.5" OD radius ensures excellent coupling on cylindrical components.
Integrated Irrigation (-IHC): Provides consistent and reliable ultrasonic transmission.
Effective 45° Shear Wave: Ideal for detecting transverse and other critical flaw orientations.
Direct Contact Design: 0 mm delay line for efficient signal transmission and near-surface resolution.
Precise Angle Control: 31° cut angle for accurate 45° shear wave refraction in steel.
Seamless Sonatest Compatibility: Engineered for optimal performance with Sonatest phased array systems.
Benefits:
Enhanced Inspection on Curved Parts: Ensures reliable data acquisition on pipes and other cylindrical components.
Consistent Coupling for Reliable Results: Integrated irrigation improves signal quality, especially during encoded scans.
Improved Flaw Detection: The 45° shear wave is highly effective for detecting critical defect types.
Excellent Near-Surface Resolution: Direct contact design maximizes signal clarity for near-surface inspection.
Increased Efficiency: Optimized design for streamlined inspection workflows.
Applications:
Phased array inspection of welds on pipes, tubes, and other curved structures.
Corrosion mapping and flaw detection on cylindrical components.
Applications requiring effective shear wave inspection with optimal surface contact.
Automated or encoded ultrasonic testing of curved surfaces.